Though these stands have been posted online before, I aim to improve upon existing internet plans to combine the squat stand and the bench press. It's more like a portable power rack at this point. Whatever it is, it's only about $50 and is strong enough to support a quarter ton, or even more.
Cost: approx. $50
Project Time: 1 day (plus drying time)
Difficulty: You have to be able to cut 2x4s, drill into 2x4s, put glue on 2x4s, drive screws into 2x4s, and mix and pour cement into a bucket containing the bottom of said 2x4s. If you can handle that, then you're good to go.
Tools Needed:- Drill
- Saw (any kind that can cut a 2x4, your choice)
- Sander (either electric or get a rubber sanding block to use by hand)
- Trowel or small shovel of some kind to mix cement
- Container in which to mix said cement
Materials Needed (short list):- 2x4 studs (you'll need about nine)
- Box of 2 1/2 inch deck screws (I like T25 star bit)
- 5 gallon buckets (two of them)
- 120 lbs. of ready to use cement (Quikrete)
- Wood Glue
- Metal Backing Plates (more info in elaborate list below)
- Twine (or some form of pliable strong rope/thread)
- Sticky Foam or Cork or something similar, and Duct Tape (optional)
- Paint / Stain (optional)
- 2 big metal "L" brackets (optional but recommended for bench press, see video at bottom)
- 2 bolts, washers, and nuts that fit the holes in your saw horse (optional, see video)
- Scrap plywood or OSB (optional, see video)
- 5 ft. length of 1 x 6 board (optional, see video)
Materials Needed (elaborate list): - 2 x 4 studs (8 ft. long each) - I needed nine for my build. It may vary depending on what you're doing with your second tier.
- Box of 2.5 inch deck screws - I prefer to use deck screws with a star bit head (T-25). They won't slip around like Phillips head screws can. If you don't have a T-25 bit, pick one up at the store for about $1 when you get your screws.
- 5 gallon buckets - You need two of these for this project.
- 120 lbs. (dry) of ready to use cement mix (Quikrete) - My estimate is that you'll need about 120 lbs. of this stuff. They sell it in 40 lbs. bags and 80 lb. bags. I got two 80 lb bags and have a little more than half a bag leftover. Three 40 lb. bags should do if you don't want to have leftovers.
- Metal Plates - click here to see a picture. There are a few options with this part of the project. I'm simply going to instruct you on the easiest way that requires the least amount of special tools or effort. You'll need 4 of the larger plates (approx 3" x 7") and 4 small plates (1" x 3"). You can find these near the lumbar with the rest of the decking/framing braces. I also show you a fancy upgraded version, for which you'll need 10 of the large plates. Scroll way down to see and decide which you like better.
- Twine - In order to "stake" down our stands while the cement dries to keep it level. Just like when leveling posts for a deck or mailbox. It's doesn't have to be twine as long as it's pliable enough to tie down your stands and strong enough to not stretch so that the stand stays level.
- Sticky foam - Like the kind you'll find in the craft section at Walmart. This is optional, and you could use duct tape as well. The purpose of this would be to avoid metal on metal contact with the bar and the backing plates. But then again most guys like metal on metal contact and the sound it makes is good because it lets you know you've hit the rack and can lower the bar. I used foam only on the small metal plates but not the large ones.
- Paint / Stain - Completely optional as it's purely for aesthetics. If you plan on painting the bucket make sure you use a paint designed specifically for plastic use. Krylon Fusion is a common choice for plastics. However, Vinyl Dye, which can be found at auto parts stores (like Auto Zone), actually soaks into plastics so it won't chip off. It smells absolutely horrible and does so for many many days, so I'd probably avoid it for this project. The better solution would be to simply buy buckets that are already a solid pleasing color, like black. Or, like I did, you could just not give a shit what the bucket looks like.
- Wood Glue - You may be able to argue this one as optional but it certainly doesn't hurt. Better to make things as strong as possible, especially when they are going to be load bearing. Even if it's just for psychological comfort.
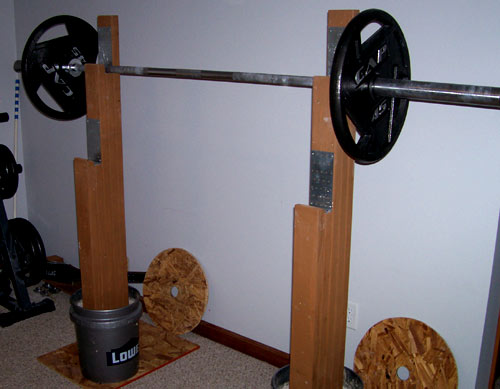 |
The top tier is for normal humans to Squat. Also useful if Mr. Fantastic wants to Floor Press. |
This is the centerpiece of your home gym. As far as I'm concerned, if you're not squatting then you better be missing a leg or recovering from surgery. There are a few different alternatives you can use in lieu of a rack or stands, such as the Steinborn lift, cleaning the weight into place, or using chairs or furniture as stands, but these are all temporary and will start to limit you on the lift when you're ready for the weight to increase, which won't take long, even if you've never lifted before. But while their name suggests their use for squats, you can use these for much more, including overhead pressing and in the case of this build, the bench press.
I did not create the idea for these "5 gallon bucket squat stands". Two people, at least, before me posted these online. However, like most projects online, they usually don't have great instructions to go off of. That's all fine and dandy for a guy like me, who has been doing this kind of stuff for 15 years. But the average person, as I've been told, will often shrug these projects off, feeling that they don't have the knowledge or skill to do it. I hope my tireless explanations of each project will help people get over that concern. If you're an adult human, you possess the motor skills to do all of this stuff. This article, will hopefully give you the knowledge you need to feel confident enough to try it.
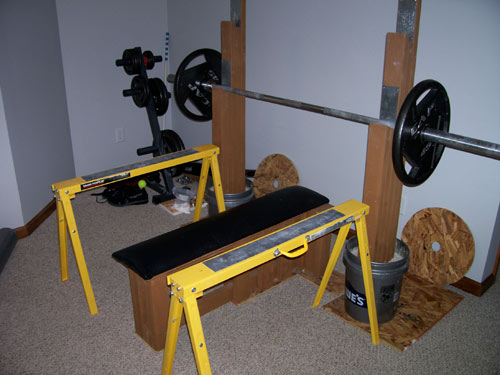 |
Bottom tier is for bench press. You could also build it higher to be a second squat stand for the shawties. |
The design I made has many additions or refinements or improvements to the basic design of these stands. My design, as featured in this article functions as both squat stands and a rack for the bench press. You just have to add a bench. I will be showing you the stands (including the second bench press tier - which could be raised to make a double squat stand if you want) in this project. To see how to make the bench go to the
Strongest Bench You'll Never Buy project.
PLANNING THE FIRST TIER (SQUATS)
First thing you need to do with any project is measure, so you'll also need a tape measure and a pencil. That kind of goes without saying in any building project. In the case of these squat stands they're not adjustable so you need to know the correct height for yourself, or whoever is going to be the one using them. It's always better for the bar to sit too low than too high. If it's a little too low, even a lot too low, You can still bend your knees to get under it. If it's too high, at best you'd have to unrack it on your tippy toes. At worst you can't use the rack at all. Unracking on your toes is a bad idea when you've got several hundred lbs. on your back. Measure it correctly, and if you're not sure, err on the side of making it shorter. If you're making a "double squat stand" that has multiple tiers for two different people of drastically different heights, start with the taller person first. If you're using the second tier for bench press, start with the squat rack first. If you're just doing a single person squat rack, then you'll just skip the part when we make the second tier altogether.
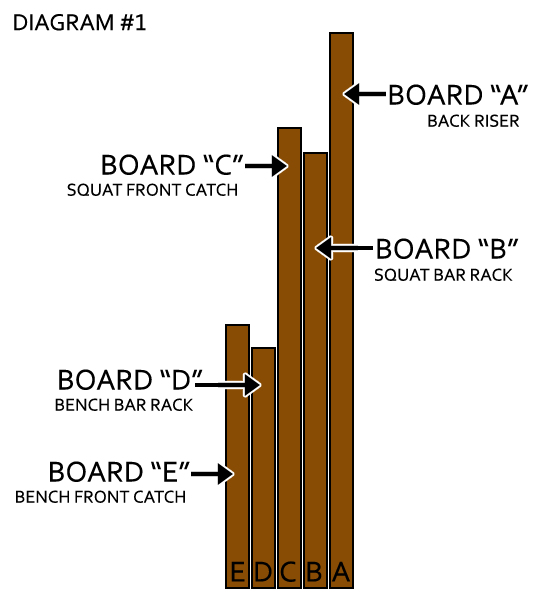
The first critical board we need to measure is the one on which the bar rests, Board B (see diagram #1). That's right, we're starting with B, because the length of all the others will be relative to this one. What I've found is that a good height for low bar squats is for the bar to be nicely nestled in your arm pit if you were to stand barefoot next to the bar on the completed rack and put your arm over it (see picture below). A bar is roughly 28 mm in diameter, which is 1.1 inches. So the measurement you want to take is from the floor to the top of your armpit when you're standing straight up. This is for low bar back squats. High bar or front squats or standing presses has the bar sitting even higher on your body so no worries there. This measurement lets you do all these things with ease. Since low bar is the lowest position you will be doing, we measure ideally for that because if that works, everything else will too.
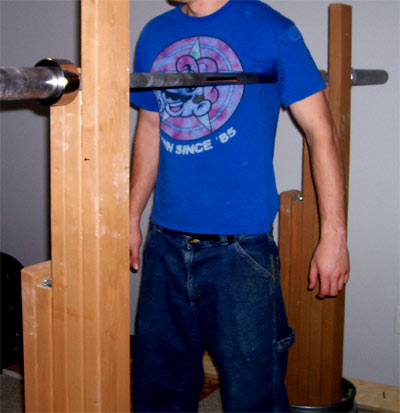
Impaled by a barbell, or just putting my arm over it? I'll let you decide.
So, measure from floor to armpit when barefoot and subtract one inch from this (to account for the bar). You can make this measurement in shoes if you wish, but remember shoes make you taller. Err on the side of making it shorter. You may opt to lift barefoot sometime so I like to measure without shoes. If you do this, then when you do wear shoes it will just mean you'll have to bend your knees an unnoticeable tad more to unrack the bar, no big deal. Since it's not adjustable better to have it be ideal for the shortest scenario, low bar back squatting barefoot. Floor to armpit minus one inch. This is the length of your first board (board B).
The next two boards are easier. Board A is the back riser of your stands. It's the tallest board that you're going to rack the bar into. If you want to ensure perfection then stand up straight and measure from floor to the middle of your neck, while wearing your lifting shoes. This is going to be the highest point you're ever going to have a bar on you either from overhead presses or high bar squats or front squats. Take this measurement (from floor to the middle of your neck) and add about 5 inches to it to ensure that the back riser is significantly higher than the bar on any lift you may be using this rack for, whether that's front squats, overhead press, or high bar back squats. This ensures you'll be able to easily rack the bar by walking it into the risers and then down. You won't have to guess if you're over the "hooks" or not. If you get a little crazy with this and make it way too tall, no problem, you can always trim it down at any time in the future. Better too long than too short on this one.
For Board C, which is the "hook" or catch part of the stand, you don't want these to be too tall. If they are you'll hit them on your way in and out of the rack. They have to be low enough so that you can clear them on a barefoot low bar back squat, which would be the lowest point the bar will be on any of the lifts you'll use this for. You're going to want these to be at least 1 inch taller than Board B, but you don't need it to be much taller than that. I'd say 2 inches taller than Board B at the most and even that is excessive. But remember, you can always trim them down after the entire rack is complete, if you notice that they're too tall. But as long as they're 1 inch taller than board B the bar isn't going anywhere. Remember the bar itself is only about 1 inch "tall". There's no consequence to them being taller as long as you easily clear them when racking and unracking your squats.
If you just want a single squat stand, and not a double squat stand for two people of different heights or the dynamic duo squat and bench press stand, then you're ready to start cutting, Make two of each board (A, B, and C) so that you'll have a pair of stands. One won't do you any good. Since you're only making the single squat stand you can skip down to the section called "Putting it Together."
PLANNING THE SECOND TIER (BENCH OR 2nd SQUATS)
If you want to add a second squat tier for another person who is significantly shorter than you, and thus can't use the same rack as you, just repeat the process for their "board B and C". The shorter tier's back riser is the taller tier's board C, which you've already measured. See the diagram and this should make sense. If your second person is taller than you and needs a higher rack tier, you weren't paying attention. You were supposed to start with the tallest person, remember?
Now, if you wanna be cool like me, you can use the second tier of the rack for bench press instead. This is a great way to save space. Both squats and bench press are major lifts you want to do. They're part of the big three (squat, deadlift, bench press). Might as well have these racks pull double duty. This will take your "squat stands" one step closer to full power rack function. In fact, when you add the DIY safety stands (we'll talk later) you'll have something that functions exactly like a power rack. If you just make these squat stands, how are you going to bench? Most people don't have a ton of space, and you probably work out alone so I think this is the most efficient design. It means you don't need space for a separate dedicated Bench Press station.
The back riser for the bench tier is already done, it's board C of your squat rack. So we just have to measure the board that the bar will rest on top of (board D) and the front catch for it (board E).
First is Board D. I'll be honest, I'm no Bench Press expert. In fact, I suck at it. Even so, I do know the mechanics involved and therefore what measurements we need to make a workable bench rack. Standard benches are 17 inches in height. As will everything in this project, making these too short, is better than too long. If it's too long you won't be able to unrack it. Too short would just mean you have to bend your elbows a fraction more when unracking.
If you already have a weight bench you can make the measurement by laying down on it and doing your best to get into position (shoulders back and tight, etc.) just like you were about to bench. Extend your arms as if you were at lockout position and act as though you are taking a wider grip (hands farther apart). A wider grip makes the bar height at lockout lower since your arms are angled outwards and not straight up. We plan and measure for the "worst case" scenario. You don't want Board D to be too high. If it's a little "too low" it's no big deal. Too high can make it unusable. So measure when simulating a wide grip to ensure if you did want to use a wide grip, there will be no problems racking the bar.
Have a friend measure from floor to your palm, where the bar will sit. This measurement is the highest point where the bar will be. You won't be able to raise it any higher without sacrificing form, so your catch (Board E) has to be less than this measurement (more on that later). So take this measurement (floor to palm when in position on the bench) and subtract about 3 inches. This is the length of your Board D.
If you don't have your bench then repeat the same procedure as above but do so while lying on the floor. Since a standard bench is 17 inches in height, just add 17 inches to your floor measurement. So if you're lying on the floor measure from floor to palm and add 17 inches. Then subtract 3 inches and that's the length you need for Board D.
If you don't have a friend to help you measure than you can make the measurement yourself by holding a pencil in one hand, as if it's a tiny barbell, point facing out (away from your face). Take your position, either on the bench or floor, but do so with your body right next to and parallel to a wall. This way your pencil head will be right against the wall. You can get into position and simply make a mark on the wall. Then measure from floor to this mark (add 17 inches if you are lying on the floor and not a bench) and then subtract 3 inches from this. That will be the length of Board D.
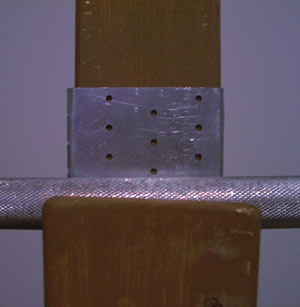
Now for the last board (board E). This is the catch to prevent the bar from falling off the front of the bench press rack. The height of this bar ideally needs to be as short as possible. Proper bench press technique requires you to tuck your shoulders back together and into the bench. As such, your arm's reach becomes effectively shorter and you somewhat "pull the bar forward more than going straight up for several inches to clear the front catch. If the catch for your rack is too high you'll need to roll your shoulders up to allow your arms to get the bar high enough to clear it. This puts you in the wrong position to press. Notice how short my Board E is (pictured left); It doesn't even cover the entire height of the bar.
There's no reason to sacrifice technique to accommodate an incorrectly built rack. Building the rack yourself means you can make any piece any length you want it. You obviously need enough height on the catch to prevent the bar from rolling forward, but you don't want much more than that. I'd say at most make board E 1 inch longer (taller) than board D. But like I said with the squat boards, you can always trim these down at any time in the future (that's what I did) so don't freak out about it. If it's too tall and you're hitting it upon racking and unracking your bench with proper form, then trim them down. But one inch taller than board D is a good standard because the bar itself is about 1 inch tall so that's enough to keep it where you want it. There's really no need to go higher than this. It's no more effective and it is just going to get in the way.
PUTTING IT TOGETHEROkay, so everything is measured. If it's not cut then do so now. I'll wait. A miter saw is probably the fastest and most accurate way to easily cut 2x4s like this. But even a hand saw will suffice. We're going to build this thing like a sandwich. For condiments we're using wood glue, and instead of toothpicks we'll use deck screws. First thing to do is dry fit it all. Lay board A on the ground first. On top of that put board B, then C, then D and E if applicable to your project. Sure up the bottom ends so they're all in line. This is what the final block of wood is going to look like.
Next we want to mark where we're going to put the screws in. To do this we'll mark on the sides. We're going to screw boards together by twos. That is to say any given screw is going to go through two boards. To do more than that we'd be in the realm of using bolts, and to do that would require we have a big ass drill bit to go through 5 boards. (okay, that's not completely true, technically speaking.) But bolts that long are more costly. If you know how to do it and want to thread bolts all the way through your 2x4 sandwich, feel free to do so. But I like to use screws. This means we have to screw the boards together one by one. That means a lot of screws, so we have to make sure they don't interfere with each other.
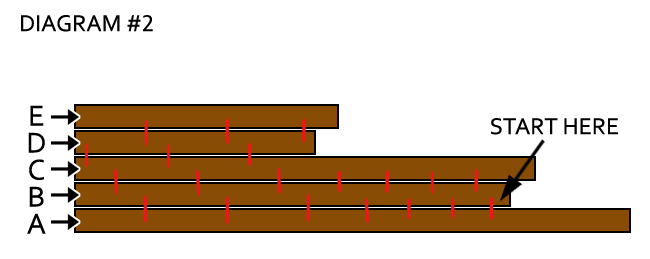
The way we're going to plan that is shown in Diagram #2 (above). Position the boards on the ground so that Board A is on the bottom and they are stacked as shown. Mark across the side of board B and board A. As shown in the pic, this mark will cover the bottom half of board B and the top half of board A. Now move about an inch to the left. This time mark across board C and B in the same fashion, this one covering the bottom half of board C and the top half of board B. Move another inch or so to the left and mark across D and C, then move left again and mark E and D. If you're not doing a two tier design you obviously omit the steps for boards D and E. Then just repeat the whole process all the way down the board. As you get to the end don't worry too much about things being perfect. Remember the bottom foot of this thing will be in cement. Just get enough screws in there to hold it together.
Notice that there is a space of one board between marks (screws) along the same plane of height. As shown below, you will put screws directly above / below others but there will be an entire board in between in which neither screw is driven into. Think of it like stairs. Mark a line, move over and up and mark another. Repeat until you're out of boards. Then drop all the way down to the bottom boards (A and B) and mark your next set of "stairs". The first "stair" and the final "stair" in a sequence will be directly over/under each other. In other words, your mark covering Board E and D and your mark covering B and A will be directly in line. If you're not doing a two tier system then you don't have boards D and E. In which case none of your screws will be directly over each other.
If I've confused the hell out of you then just remember it's not brain surgery. We're putting screws into wood. All we need to do is hold it together and make sure the screws don't bump into each other. Whether you do it exactly as I've laid out or not it doesn't matter. Just get enough fasteners into the wood to make it solid and stable.
Now you take the boards off one another and keep them facing the same side up as they were. Go ahead and put a mark on the top so you know which side is up. We're going to pre drill holes rather than just drive the screws in. This will ensure that we don't split the wood. Find a drill bit that is smaller than the width of your screws. If you drill the holes too big the screws won't have enough wood to screw into. So pick a drill bit that you can clearly tell is smaller than your screw width (the shaft, not the head).
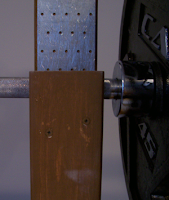
Take Board B and put it on top of Board A. Make sure the bottoms are lined up. You're going to drill through them both so make sure it's all square since this is going to be how they're screwed together. Look at your marks on the side of Board B. You'll have two types of markings. One that covers the top half of the side of board but not the lower half, and those that cover the lower half but not the upper half. The ones that cover the lower half will also extend onto the top half of board A. These are the marks that you're going to drill. Confused? See Diagram #4 below. Leave the other marks alone for now.
I recommend putting two holes on the face of each board, in line with each of these marks (see picture). Now your drill bit may not be long enough to go far enough into the bottom board, in this case board A. That's fine. Just make sure as you load it into your drill you keep it long enough to get a little bit into the bottom board.
Drill straight down through board B completely. You'll end up going into Board A a little bit. Repeat this procedure, putting two holes for each mark on the board. Then you'll have to take board B off of board A. There will be shallow holes through this board. All you have to do is deepen them. To know exactly how deep, put a screw against the side of two of the boards. Notice how far it goes into the bottom board. This is roughly how deep you want to drill the holes in that board. It doesn't have to be exact but that gives you an idea.
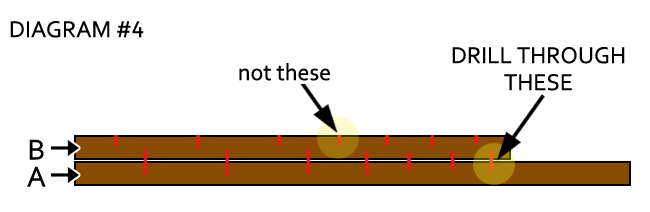
After you have all the holes drilled to connect B and A get your wood glue. We have to assemble this like a sandwich one board at at time. Slather board A with glue, then put board B on top of it. Line up the edges. Now start driving your screws through the pre-drilled holes. Everything should line up perfectly and they'll go in with ease. Drive the screws in until the heads are forced into the wood slightly. This is called counter sinking and decking screws like this will do it naturally in softer wood like 2x4 studs. Just counter sink them a bit so that the heads are not sticking out of the wood. Don't sink them too far in. We just need the board flat so it rests against the next board nicely.
You should also have a towel or something to wipe up the glue as it will get squeezed out between the boards like too much mayonnaise on a turkey sandwich. Now Boards A and B are completely secured. You're going repeat the entire process with the next board. So put board C on top of board B, line everything up. Then drill through board C according to your marks, just as you did before. Take board C off, deepen the holes on board B. Slather B with glue, put C back on and screw it down. Repeat again and again for D and E. Now you've got the wood all secured together. Repeat the entire process for the other stand. Let them dry for a few hours. If you're too impatient, it won't be the end of the world if you continue on immediately.
EXIT WOOD, ENTER STONEOnce ready, it's time to mix the cement. Follow the directions on the bag. It's not rocket science. You're mixing the powder in the bags with water until it's the proper consistency, again read the label. Because you're not mixing a lot you can use a hand shovel / trowel to mix it. It may even be better to have a smaller tool to do so but I'm sure a large shovel would work just fine too. I'd recommend you put something down over the area you're going to be mixing and pouring; An old sheet or plastic drop cloth is fine. Put your 5 gallon buckets and mixing container on the sheet. I'm assuming you're doing this on a surface like your garage.
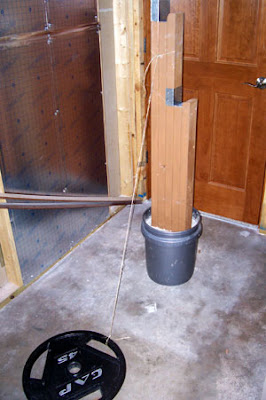
Stand your wooden posts up in the buckets and center them. Now start shoveling your cement into the buckets. Fill the buckets up. Leave an inch or two at the top. Like I said, this is going to take about 120 lbs. of dry mix, maybe a little less. The wood studs sit directly on the bottom of the bucket which sits on the ground. Since gravity pulls straight down, the force it transmitted from the barbell through the wood, to the ground. The main job of the cement is to hold the studs upright and make them bottom heavy so they won't tip. In other words, the cement isn't actually load bearing, its function is in stabilization.
The way you'd typically brace a post in cement like this would be to put stakes in the ground and tie ropes to the post on each of the four sides ensuring that it cannot move. But to do that here you'd have to find a pretty flat level spot to put the bucket in your yard.
If you have enough heavy weights or other heavy objects you could do the same in your garage. But rather than using stakes in the ground, tie the rope to the weight plates instead. Tie a heavy plate to each side of the stand, (4 sides 4 plates) pull them tight and adjust them until the stand is level both front to back, and side to side.
After you get them level, just let the cement dry for a few days. Resist the urge to use them as soon as you think you can get away with it. Let it sit for 48 hours. Now that the cement is dry the stands are usable. However there are a few more alterations we can make to improve the function of our stands.
ROUND > SQUAREFirst is to round the inside edges of the bar catches, that is the stud that sits in front of the bar to prevent it rolling forward (Boards C and E). You don't have to do this but it does open up a little more room when lowering the bar back onto the rack. It also encourages the bar to roll into the rack if you happened to put it down on the front wood catch. There's plenty of room to rack and unrack the bar and I've yet to have any trouble but nevertheless there's no reason not to do this, is there? To get the curve you could use a router but really all you have to do is cut the corner straight off. Any kind of hand saw will do.
Of course this will not leave you with a rounded edge. To remedy that use a sander with a heavier grit paper. You can do this by hand as well if you have a rubber block. You may have to do it by hand unless you have an electric sander small enough to get in there. Just work the edges until it's rounded nicely to your liking.
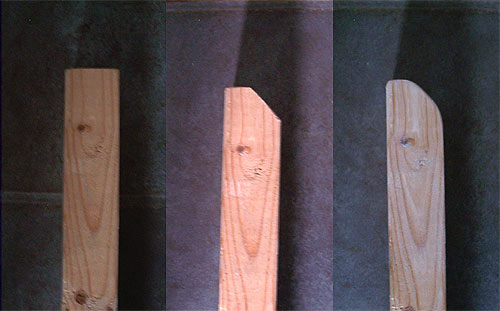 |
Rounding the tops of your front catch pieces functions better and looks prettier. |
Since we've got the sand paper out, might as well clean up all the edges to take off any sharp corners and splinters. It doesn't have to be a perfect finish job, unless you want it to be. Just make it safe by eliminating any rough edges.
Now is the best time to pretty it up and paint it if you choose. Any kind of paint will do. If you're buying paint specifically for this don't get too much. A quart is typically the smallest size in which you can really get paint, and even that will be more than you need even if you give it several coats. If you plan to stain it then a small pint can should be enough. If you did paint it, let it dry fully. If you stained it, it will be dry enough to continue in much less time since stain soaks into the wood you can continue even when it's not completely cured.
HEAVY METALThe next alteration is to put metal plates where the bar is going to contact the wood. If you don't do this the bar will eventually wear away at the wood. I'm not saying it will get so bad as to compromise the integrity of your stand but with a simple metal plate you can remove the issue entirely. There are many ways to accomplish the task. Most involve cutting and/or bending metal. It's not such a big deal but when choosing which to include in this article I opted to keep things simple.
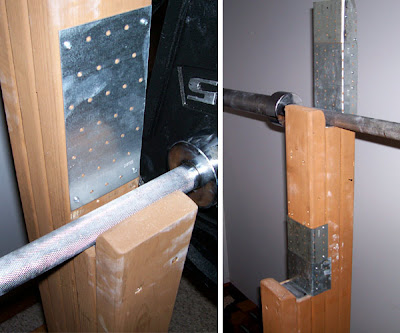 |
If you choose the simple version (left) put the plate all the way down, unlike shown in the picture. |
The simple version is to merely take the store bought metal plates, put them against the wood (Boards A and C) and slide it all the way down so that its bottom edge is in the corner between back riser and where the bar sits on top of Boards B and D. If you leave a space of open wood below the metal plate (like shown in the picture), the bar will eventually wear away at it. Then either put in small screws or nails through the holes in the metal plate to secure it. One in each corner is enough
If you choose the fancier version, as shown above (right), you have some work to do. You have to bend your big metal pieces into three sided brackets as shown in the picture to the right. You can accomplish this by measuring your plate against a 2x4. By bracing it against a block of wood (2x4) you can start to bend it mostly by hand. But you'll have to use either Vice Grips, a hammer, or both to really finish it off and get a sharp 90 degree bend.
For the squat risers, the sides of these brackets will be too long and hang off the 2x4. It would not be a big deal but the corners of these things are not exactly made of cotton balls. To ensure you don't scrape yourself on them, use your hammer to bend them around the back of your risers. This eliminates the need to cut the brackets to perfect size, which can be a time consuming event. You don't have to worry about this for the second tier, for obvious reasons.
The picture to the left isn't an exact step by step process but gives you an idea of the technique involved. With these " [ " shaped brackets you can stack them one above the other to cover the entire height of your back risers. You can now also fasten them with screws from the side. The benefit of this is that the screws are not ever going to touch the bar and potentially scratch it. This is the version I use on my stands at home.
Another way to accomplish this is to use metal "flashing" This is thinner metal that you can cut with tin snips or even garden sheers. Bending it is also easier. You'll still use the block of wood technique where you use the wood as your shape and your hands and hammer to shape it to the block. With flashing you'll be able to use a single piece to span the entire height of your riser. And you'll be able to drill and screw through the sides to keep your front piece completely clear. I haven't priced flashing so I don't know which of these ways is the cheapest. But I figured that this idea bears mentioning as well. As I said, there are many ways to go about this. You can choose whichever you fancy most. I used the "simple" version for 6 months and saw no issues with it.
Now for the bottom plates. Take your small (1 x 3") metal plates. Put them onto the top of Boards B and D). Drive two screws into them, diagonal from each other, as shown below. Now you can cut out a piece of craft sticky foam and stick it on top of the plate. This design does a few things: First, the metal plate protects the top of the wood so it doesn't get smashed and splintered. The position of the screws acts to help keep the bar centered. The foam protects the bar from metal on metal contact with the screws and it also furthers the centering of the bar as over time the bar creates a groove by smashing down the foam.
However, I have noticed after years of use that this design can scratch your bar. To prevent this see some suggestions below.
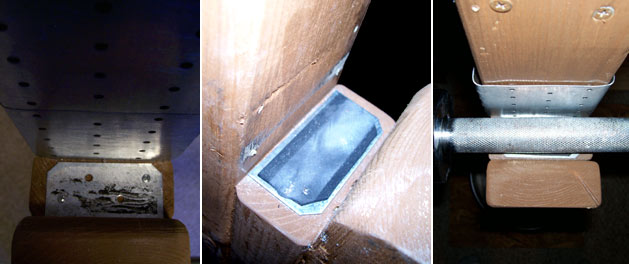 |
With this design the bar will find it's groove and stay in the center of the "hook." |
Another option is to use cork instead of foam. Creating a ring of double sided tape via duct tape and sticking it to the back of a piece of cork, also works. This is much thicker and doesn't crush like the foam. You could also buy a longer piece of metal (perhaps flashing material) and bend it down the sides and mount it via screws from the side.
CONGRATULATIONS
There you have it, a pair of squat / bench press stands. Each one will weigh in the neighborhood of 80 lbs. You can move these relatively easily, especially after you begin using them to develop your strength. When you're squatting and deadlifit hundreds of lbs. 80 lb. stands are not a big deal. So you can move them out of the way when not in use, if you don't have a dedicated space to keep them out. They are completely bottom heavy and therefore won't tip over or slide when you rack and unrack the bar. The amount of tilt you have to get before these things will fall is enormous. It will never happen by accident and you'd be hard pressed to do it on purpose, if you have a loaded bar on your back.
I have, as of yet, tested these with a load of 450 lbs. They handled it with ease. The compression strength of the materials , given the way gravity will put the force, can handle more than a, literal, ton; a weight that you'll never squat. And if you're ever squatting even near half that, say 1000 lbs. I think you could probably swing to buy a high quality commercial setup; which is not to say that you would have to. Wood is strong. Your house is likely made of it, as is your deck. And a well put together wood product is better than a flimsy cheap metal commercial product. It's a cheap material that's easy to work with and in the right configuration is strong as all hell.
Here's a video with a few upgrades. I've used these stands for about 2.5 years with no problems but here are two things I recommend you do from the start.
This was a long post. I hope I've covered everything. If you have any questions, leave a comment and I'll do my best to answer them.
- Carl